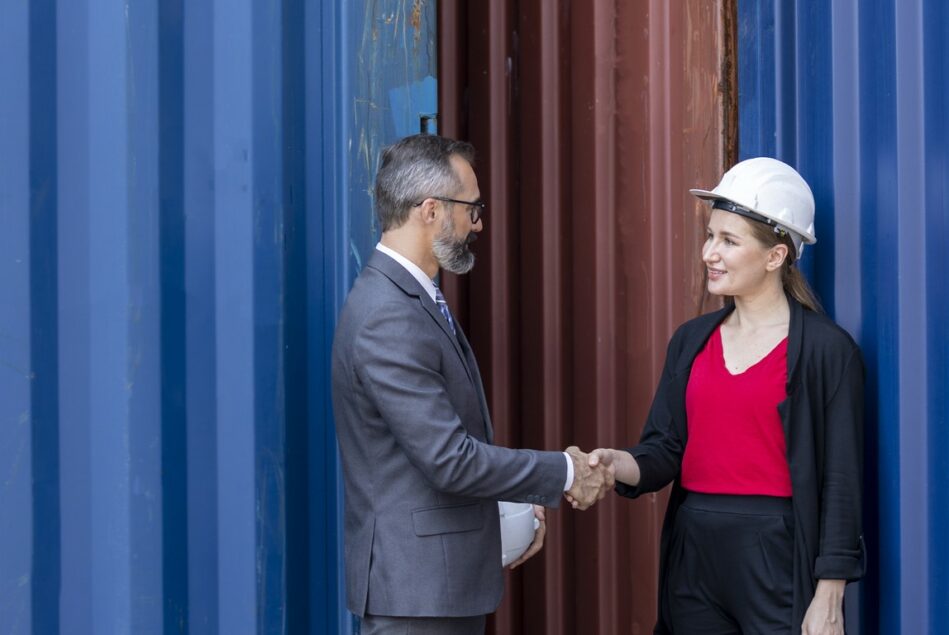
Supplier management is one of the most challenging aspects of product development. Many companies still rely on siloed processes, where design information is shared via unstructured communications and exchanges of disconnected documents. The result is delays, errors and missed opportunities. As supply chains grow increasingly complex, seamless collaboration between engineering teams and suppliers become ever more critical.
By enhancing collaboration with suppliers during the design phase, companies can significantly improve efficiency, quality and speed. Yet true success depends on adopting modern, integrated strategies that go beyond basic transactional exchanges. Real collaboration happens when there are well-defined processes for continuous flow of accurate data, open communication, traceable decision making and mutual trust among all parties.
Traditionally, engineering teams and suppliers interact in an ad hoc, inefficient manner. Suppliers are often excluded from core engineering workflows, forced to rely on fragmented and difficult-to-trace communication methods like e-mail and phone. This disconnect makes it difficult to access up-to-date project information.
This becomes particularly problematic when last-minute design changes, manufacturability issues or quality concerns arise, as they frequently do in complex industries such as manufacturing, aerospace and automotive. Without a structured, traceable method for managing exchanges, the risk of miscommunication and errors increases.
One of the most effective ways to address these challenges is by creating a real-time, transparent environment for collaboration. When buyers integrate suppliers early and directly into the product-development process, the parties don’t have to rely on disconnected communication methods. All have access to the latest, most accurate information.
Two Essential Tools
The solution involves two key components:
- Product lifecycle management (PLM) platform. This serves as a central location where supplier-related data, such as contact details, performance scores and part information, is structured, easily accessible and consistently managed. It ensures that all interactions remain traceable across departments, fostering a more informed and collaborative workflow.
- External collaboration portal. This is a secure portal that provides suppliers with real-time access to critical data, such as design specifications, the latest changes and production updates, while maintaining a direct communication channel with engineering teams. Suppliers and engineers can address design or supply issues within the system, reducing delays and errors.
When a design or process change is required, it must be communicated quickly and accurately to all parties involved. Traditionally, this process has been slow and error-prone, relying on manual updates and fragmented communication.
Improved collaboration between suppliers and engineers not only streamlines communication but also ensures design issues are addressed early. When suppliers are integrated from the start, they gain a clearer understanding of expectations and can proactively identify potential issues before they escalate.
By enabling collaborative change management, companies can significantly shorten development cycles and accelerate time to market.
Need for Security
As collaboration with external suppliers increases, so does the need for stronger security and access control. Sensitive information must be protected, ensuring that only authorized individuals can view or edit it.
Access should be tailored based on the supplier’s role, specific tasks and need to know. For example, only certain teams within a supplier’s organization may need access to CAD files, while procurement teams might only require pricing or logistics information. Secure data-sharing platforms enable controlled access, allowing suppliers to view only the relevant information necessary for their tasks, while safeguarding critical company data and intellectual property.
Effective collaboration transforms suppliers from transactional vendors into true partners in product development. The key is integrating them early in the development cycle, providing real-time access to information, and empowering them to contribute to key decisions.
By addressing potential issues early, supply chain partners can minimize costly errors and enhance product quality through joint problem-solving and informed decision-making. Additionally, better visibility and coordination reduce supply chain risk, creating a more resilient and efficient development process.
Today, engineer-supplier collaboration is a strategic necessity. When suppliers are fully integrated as true partners, the benefits are clear: accelerated development, improved quality and a more resilient supply chain.
Paweł Z. Chądzyński is senior director of strategic research with Aras.