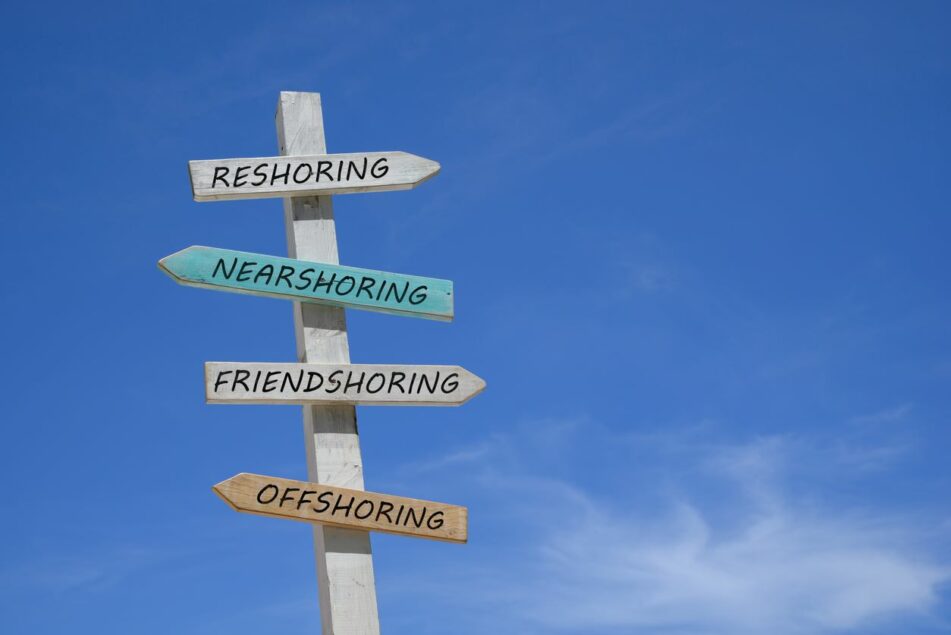
Nearshoring, considered a cost-effective solution for businesses seeking both cheaper labor and faster supply chains, has taken on new complexities in the current global climate. With rising labor costs and disruptions to traditional supply routes, companies are re-evaluating the advantages and challenges of nearshoring — especially when it comes to cross-border trade between Mexico, the U.S. and Canada.
Historically, the primary advantage of offshore manufacturing has been its cost-effectiveness. By shifting operations out of the U.S., companies were able to capitalize on cheaper labor. Today, however, it’s no longer just about labor cost. The decision on where to make product has become more nuanced.
One of the key advantages of nearshoring is the potential to shorten lead times. By moving production closer to home, companies can bypass long ocean freight routes and avoid the unpredictability of international shipping, involving skyrocketing freight costs and port disruptions. Ocean freight prices, which soared from $2,000 per container to $25,000 during the COVID-19 pandemic, have made businesses rethink their reliance on distant production hubs.
While companies continue to face challenges related to raw materials and certain components still being sourced from Asia, nearshoring can reduce their dependence on long and unpredictable transportation routes. This shift can, in some cases, help businesses navigate some of the volatility in the global supply chain.
The Logistics and Supply Chain Dilemma
One of the key hurdles to nearshoring is the availability of raw materials and the supporting components needed for production. In industries like apparel, manufacturers still rely on suppliers from Asia for essential materials such as zippers, trims and fabrics. Even if a company nearshores its assembly in Central America or Mexico, it must still source and transport some items from more distant suppliers, incurring additional logistical costs and risks.
Additionally, there are inherent risks in transporting valuable goods across regions with less stable infrastructure. For instance, transporting products through Mexico presents a security risk due to the possibility of theft and loss, especially as goods move deeper into the country. The complexity of these logistics challenges further complicates the nearshoring decision for many companies.
Then there’s the tariff situation, which is affecting nearshoring decisions in both the short and long terms. While such agreements as the Central America-Dominican Republic Free Trade Agreement (CAFTA) could provide duty advantages, the scrutiny surrounding the United States-Mexico-Canada Agreement, along with potential changes to tariff policies, makes the landscape unpredictable.
As trade regulations shift, and shift again, companies must constantly reassess how nearshoring fits into their broader strategy. The government’s role in influencing supply chains and trade patterns has added another layer of complexity. Changes in leadership or policy can quickly alter the feasibility of certain nearshoring initiatives, leaving companies grappling with these changing dynamics.
There are two primary types of nearshoring: cross-border movement of finished goods, and true nearshoring of manufacturing. Each has its own set of benefits and challenges. The first option presents a relatively straightforward model with fewer logistical issues. However, true nearshoring, where companies move manufacturing operations to nearby regions like Mexico or Central America, requires a deeper understanding of raw materials, labor costs, local policies and infrastructure.
For instance, in industries such appliance manufacturing, where products have relatively simple components and high-volume production, nearshoring in Mexico can be an effective solution. By contrast, more complex products such as apparel may not be as viable for nearshoring in the Western Hemisphere. Again, most raw materials needed for apparel production are often sourced from Asia, and even if manufacturing takes place closer to the U.S., transportation and logistical challenges remain.
Weighing Costs and Benefits
When weighing the question of whether to nearshore, companies need to assess each decision on a commodity-by-commodity basis. For some products — for example, basic consumer goods like denim jeans — nearshoring may make sense due to the relative ease of sourcing materials from nearby countries. For others, such as complex electronics or high-tech machinery, the higher cost of labor in nearby regions may outweigh the benefits of reduced transportation time and costs.
Companies must also consider their broader risk exposure. Many businesses that previously relied heavily on Asian suppliers have begun making moves to distribute that risk by diversifying their supply chains. A shift to nearshoring can in some cases help mitigate the risks associated with over-dependence on a single region, particularly in light of the ongoing trade tensions with China and the broader volatility of global trade.
Companies today are navigating a complex web of factors, including the availability of raw materials, trade regulations, labor costs, and the risks associated with transportation. While nearshoring offers advantages such as shorter lead times and reduced exposure to ocean freight volatility, the situation is changing on an almost daily basis, and the benefits are less clear-cut than they once were.
As businesses adapt to these changing trade dynamics, the outlook for nearshoring will depend on a combination of factors, from geopolitical shifts to how companies innovate around supply chains. What was once a simple cost-cutting strategy is now a multifaceted decision around numerous variables, logistical, political and economic.
Kenneth Cochran is a managing director of Alvarez & Marsal’s Consumer and Retail Group.